Pressures, Case Strength and Back Thrust
By Bob Jourdan
©Copyright 2010, Precision Shooting Magazine
All handloading manuals take safety very seriously. They cover most of the hazardous points in reloading ammunition in an effort to keep a beginner out of trouble. Some go into detail concerning the strength of brass cases and the importance of using the proper case for the proper loads. They also have some discussion of chamber pressures, advising reloaders what to watch for as they approach top loads that could result in problems. This is all usually done in a good manner, but of course it does not get into deep, technical detail, nor should it. These books are written for reloaders, experienced or beginners, and often refer the readers to other more technical books and manuals for greater detail on the subject. As we all know, any average intelligent shooter can become a proficient ammunition reloader and enjoy the hobby for a lifetime. But as with any consuming hobby, the quest for more knowledge and advancement comes all too soon. Continued success with common factory cartridges often leads the curious minded to start looking at wildcats or improved cartridges, and even the development of some new, personal design that will send off their favorite bullets at the speed of light...or faster. At this point the shooter must investigate the possibilities of case failure and the consequences of excessive chamber pressure.
Two extremes, the .300 Weatherby Magnum, (L), and the old-time .30-30 WCF, (R). Notice the thickness of the case web.
One of the most important developments in firearms history was the brass cartridge case that first came onto the scene just before the Civil War. In 1856 a dentist named Maynard patented a brass cartridge case that would expand when fired and seal the rifle chamber to close off any escape of powder gases. This forced all pressure to push behind the bullet and send it out the barrel with the best velocity. Sealing of the chamber was a major step in the development of breech loading rifles. Prior to that, all breech loaders spit a lot of fire and brimstone out the rear of the action into the shooter's face.... They were not any too popular in those days.
With time, shooters wanted more velocity which meant more pressure. When smokeless powders came along in 1886, first in France and then all around the world, pressures began a steady move up. By the turn of the century they had reached the 50,000 c.u.p. (copper units of pressure) that is common today. This copper unit of pressure is simply a description of how chamber pressure came to be gauged by use of a crusher gauge, invented by Alford Noble in about 1860. Small carefully controlled cylinders of soft metal, copper, called "crushers" are placed in a tool attached to the chamber area of a rifle barrel where a hole has been bored through the chamber wall and side wall of a cartridge case. When the cartridge is fired, the high pressure gases push a small piston in the tool up against the copper cylinder, compressing it to some degree. The copper crusher is then measured and the amount of crush length is compared to a compression table to arrive at the pounds of pressure required for that amount of copper compression. Then we use the term, copper units of pressure to relate it to the shooting world.
Here we have the .22-250 Remington, (L), and the .30-30, (R). The .22-250 has a two-thickness web, .218" at the outer interior diameter and .195" in the center area about equal in diameter to the primer pocket.
Even though we still use the c.u.p. term for chamber pressures in many publications, there is now an improved system giving pressures in pounds per square inch (psi). It uses electronics to arrive at pressures and is called an electronic-transducer gauge. Instead of crushing a copper piece, a special quartz piece is used because quartz has the property of generating an electrical charge when subjected to mechanical force. This is now known as a piezoelectric transducer, and many loading manuals now list pressures as psi. As reloaders, we must be aware of the significant pressure differences between c.u.p. and psi, with the psi always being much higher. An example would be a .30-06, 150 gr. bullet at 3005 fps for 45,900 c.u.p. or about 58,000 psi. This pressure difference of 12,100 pounds requires your attention. Don't mix c.u.p. with psi.
Good rifle design became very important to contain this pressure, since all chamber seal was provided by the relatively thin brass case. And brass simply can't handle pressures as high as steel can. From this, shooters can see why it is commonly stated that the weak point of any rifle is the brass cartridge case. In a properly designed rifle, the cartridge case will protrude out of the barrel at the breech by about 1/8" before reaching the bolt face. In bad set-ups the distance can be as much as 1/4". With an open gap like that it is easy to see that 50,000 c.u.p. inside the thin brass case can blow it out and release the pressure in the action and shooter's face. Thus, any gunsmith knows, or should know, that the deeper the cartridge is seated into the full cover of the barrel, the safer will be the rifle. Naturally, there must be a way to hook an extractor over the rim of a cartridge to withdraw it from the chamber, and this is where the difference in case head protrusion has to be considered. A large and poorly designed extractor will require the case head to protrude more than would a small, well designed extractor. And in some rifles an extractor cut is required in the barrel. If this cut is made too deep, the cut will expose the thin sidewall of the cartridge case and set up a possible blowout.
It is often stated that a certain case is built stronger than another. In many instances this is true. But in others, it is not. Usually the original cartridge will be designed to handle the pressure of that one particular load. For example, the original .30-30 Winchester cartridge case is designed for pressures in the range of 40,000 c.u.p. This means that the brass is sufficiently thick to handle that amount of pressure in original .30-30 rifle designs. By carefully sectioning the head of a .30-30 case the solid web thickness can be measured and compared to the web thickness of other case designs. My recent measurement showed the .30-30 web to be approximately .182" thick, which means that anytime a cut is made in the barrel breech that exposes more than .182" of the case, the thin wall of the case is all that will be left to hold that 40,000 c.u.p. If a gun designer made a cut of .200" or so to make room for the extractor in the barrel breech and used the .30-30 cartridge case, a disaster would be in the making....
Since the .30-30 was reputed to be a rather weak case, I decided to section a few others to compare their web thicknesses. The .30-06 case showed a web thickness of two dimensions in a Remington case. The center, approximately the diameter of the primer pocket, measured only about .190" thick, while the remainder of the web measured .202". Why they thinned the center around the flash hole, I do not know. Nevertheless, this indicates that any case protrusion of more than .200" from the barrel should be considered dangerous. The maximum product pressure for the .30-06 is listed as 53,200 c.u.p., and that would be exciting if it got loose in the action of your favorite rifle. Since this is a rimless case it is common for the case head to protrude from the barrel breech by some amount, and a few rifles do have a cut made in the barrel to let in an extractor.
A popular varmint cartridge of the day is the .223. It is designed for a maximum product pressure of 55,200 c.u.p., a little hotter than the .30-06, but the case web measures only about .192" thick. This might seem a little inconsistent when compared to the lower pressure and thicker web of the .30-06, but the area inside the .223 case is much smaller than inside the .30-06 and this results in less real pressure working back against the bolt of the .223 in the form of back thrust. The inside chamber pressure is high, however, and therefore the .223 case must be kept to less than .192" unsupported protrusion out of the barrel for safety.
(L-R): .270 Winchester; .30-30 WCF; .22-250 Remington; 6mm BR Norma. The web thicknesses are .202", .182", .218" and .162", respectively.
When I cut into the .300 Weatherby belted case, I expected to find a very thick, substantial web. It turned out to be only a little thicker than the .30-30 and the same as the small .223, measuring .192" thick. Next, I sectioned a .264 Winchester case, made by Winchester, and found it to measure .215" thick at the web and about .200" near the flash hole. It is interesting to find that belted magnum brass may not be any thicker at the web than .30-06 brass, and the chamber pressure of the .300 Weatherby is listed in various places as something around 57,000 c.u.p., or about 7% above that of the .30-06.
A favorite wildcatter's brass is the .284 Winchester rebated case. The web turned out to measure slightly thinner than that of the .30-06 at about .200" thick. Since it is a rimless case, headspacing in the same manner as any other rimless case, it would present the same potential problems with one other added in. That is the fact that it is of the rebated rim type where the rim is the same diameter as that of a .30-06, but the body is much larger starting just ahead of the extractor groove. This will create a larger internal head area which leads to higher back thrust on the bolt when compared to smaller diameter cases with the same chamber pressure. The chamber pressure for the .284 is listed at 57,200 c.u.p., about the same as the .300 Weatherby and the .264 Winchester.
The next case I used for this investigation was the popular benchrest case, 7mm BR, originating from a straight bodied .308 and later from a .300 Savage case. This case is commonly necked down to .25, 6mm or .22 for use in benchrest rifles where pressures are habitually run up considerably above 55,000 c.u.p. The web turned out to be much thinner. My measurements showed the thickest part measuring about .196" and the thin part around the primer pocket only .180" or so in Remington brass. The Norma BR measures only .162" web thickness, and the Lapua BR is .168".
The case on the left is a .270 formed into the 6.5x06 Ackley Improved. Notice the stretch valley just in front of the solid head. The .22-250 case on the right shows no stretching, no thin stretch valley near the web.
These case web measurements are not too informative when we consider that all have been used extensively for wildcatting and all have been successful even with unknown pressures of more than 60,000 c.u.p. This seems to lead to the conclusion that the main concern might well be the method of chambering each wildcat cartridge. If the cartridge is well contained inside the chamber with only a minimum cut for the extractor, it will work well with very high pressures.
Back thrust, mentioned above, brings us to another consideration for cartridge cases used in experimentation or wildcatting. Even though we read of the chamber pressures being in the 50,000 c.u.p. range in most high powered cartridges, it has been proven that back thrust on the bolt is retarded by the fact that the case wall expands to grip the chamber wall, thus holding the case from backing up hard against the bolt. This also indicates that the case head will hold a great deal of pressure by itself, and this is where the web thickness becomes very important. If the gap between the bolt face and the barrel breech is wider than the thickness of the case web, the high chamber pressure inside the case will blow through the thin sidewall in the unsupported gap area. And while we all hear of rifles blowing up, that is not the case. It is rather the loose pressure blowing out from an unsealed chamber when a case failure occurs. As long as the 50,000 c.u.p. plus can be retained inside the chamber, receiver ring and barrel, it is rare that a failure occurs. Steel will contain much more than 50,000 psi, and tests on actions and barrels have proven they will hold more pressure than will the brass case that seals the pressure off. Actions have been tested far beyond 75,000 psi with no failures. The brass, however, will begin to flow at something over 70,000 psi, and will totally fail by the time the pressure reaches 80,000 psi. Then the release of all that pressure inside the receiver, down through the magazine, back through the firing pin hole and into the bolt body is enough to split the stock into kindling wood...among other things. I have the remains of a Mauser M98 action that was totally destroyed with a standard loaded .22-250 cartridge when the headspace became too long, allowing the case to separate. The brass cartridge head was welded into the ejector slot in the locking lug and part of the case body at the end of the web area expanded and formed between the bolt face and the butt of the barrel in a tight manner, looking a lot like it had been melted and poured into the gap. I had to remove the barrel in order to open the action. Incidentally, the shooter ended up in the hospital emergency room for removal of metal and carbon fragments, his eyes being saved by the glasses he was wearing. All of this was brought about by the failure of the brass case when the soft M98 locking lug seats finally pounded back far enough to make the headspace too long. Perhaps I should add here that Mauser actions are not heat treated like our modern factory actions. They are made from relatively soft carbon steel and then only surface hardened, case hardened, for a very thin, hard surface. When these M98s are reconditioned many shops will lap the locking lugs and often will cut the thin, hard surface completely away, leaving only the soft carbon steel underneath to hold the pounding of the bolt locking lugs in the future. They will pound back over a period of time resulting in too much headspace and a wrecked rifle...or worse.
The amount of back thrust on a bolt can be changed to some degree by the design of the cartridge case. Cartridges with considerable taper in the body will produce much more back thrust than will a more straight walled case. To prove this, P.O. Ackley tested the very tapered .250-3000 cartridge in a lever action Savage M99 rifle by loading it up until the case became difficult to extract. This occurred with a load of 34.5 grs. of powder and a 100 gr. bullet to produce a velocity of 2900 fps. At 36 grs. of powder, the action became frozen and required the use of a rod to pound down the barrel while pulling hard on the operating lever to get it open. He then rechambered the rifle for the almost straight tapered case of the .250-3000 Ackley Improved cartridge and loaded it with 36 grs. of powder and a 100 gr. bullet, the very load that previously froze the action. Upon firing, it extracted very easily. He then continued to increase the load until reaching 42 grs. of powder for a velocity of 3400 fps. The action still opened easily. Thus, he had removed most of the back thrust that had originally frozen the action with the tapered, standard case and was able to radically increase the velocity, along with the pressure, without an increase in back thrust by simply removing most of the taper from the case. Today, most experimenters use cases with very little taper for their wildcat creations.
Another interesting test by Ackley was with the .30-30 Ackley Improved cartridge in a M94 lever action Winchester. He found a dry chamber would allow the cartridge case to firmly adhere to the chamber walls; the rifle could be fired with the locking lugs completely removed from the action and only the lever left to hold the bolt shut. The straight walled case did not back out of the chamber, proving that back thrust had been almost completely eliminated by the cartridge case design.
Back thrust is normally figured by multiplying the chamber pressure by the internal area of the cartridge head. It does not equate to chamber pressure as most shooters might think. If it did, then the back thrust of the .223 and the .460 Weatherby would be the same because both are loaded to a chamber pressure of about the same, 55,000 c.u.p. In reality, the .223 has a back thrust of only about 4,025 pounds, while the big .460 has 10,425 pounds, even though the chamber pressures are about the same. Thus, it is readily seen that when given a choice we would much rather have the 4,025 pound load on the bolt face, right near our head, than the 10,425. And this is exactly why we should consider the case we plan to use for our latest wildcat design.
In any chamber the only two parts of a cartridge that are not in some contact with the chamber are the primer and the bullet. The bullet has the barrel opening directly ahead of it, so it will move forward rather easily upon firing the round. The primer is held in the head of the cartridge, in the primer pocket, with only a little friction to secure it. When the cartridge is fired the full pressure developed within the cartridge case will be pushing forward on the bullet base and backward on the case head creating what we call back thrust. Back thrust through the small .080" flash hole has been calculated to be in the 600-800 psi range, and of course the bolt face should be snug against the case head. The primer should be seated slightly below the case head and the initial pressure through the flash hole will push the primer back into solid contact with the bolt face. The pressure inside the case will also work against the case wall to expand it out against the chamber wall. This will cause the case to adhere to the chamber very tightly, preventing the case body from moving back as much as will the case head. Naturally, this results in stretching the brass case slightly and can lead to case head separation. And now, because the bolt and barrel do not make positive contact, it is readily seen that the brass cartridge case head is retaining at least some pressure to prevent it from blowing out in the barrel-bolt gap. Since force is a factor of effective area times pressure, by knowing the area of the inside of the case head we can calculate an approximate back thrust pressure for each cartridge. I say approximate because it would be difficult, if not impossible, to determine back thrust restriction caused by the cartridge case form and adherence to the chamber wall. In other words, back thrust is contained by a combination of the bolt locking lugs and the case clinging to the chamber wall. Ackley's experimentation along these lines proved that a properly designed case will hold back a surprising amount of back thrust from the bolt and locking system of a rifle, but only when the chamber is kept dry. By oiling the chamber or cartridge case before firing, back thrust will be increased tremendously, and may even approach that of full chamber pressure.
Below are examples of back thrust calculations for three cartridge head diameters with equal chamber pressures of 50,000 c.u.p. The chamber wall friction resulting from case configuration is ignored for ease of calculation, and these back pressures are considered to be maximum (see table below).
From this chart it is easy to see that if you plan to use a belted magnum case for your wildcat cartridge, it will produce more than 20% additional back thrust when compared to using a .30-06 case loaded to the same 50,000 c.u.p. chamber pressure. Another way of stating it is that you could increase the load in the .30-06 case to a chamber pressure of 60,000 c.u.p. and still have less back thrust on your bolt than if using the magnum case at only 50,000 c.u.p. And this is one reason why it is so often fruitless to use the belted case for your brain child, lightning striking wildcat....
In recent years the ammunition companies have been avoiding the use of belted cartridge cases for new magnum designs. They have moved to the smooth bodies, no belts, of variations of the old .404 Jeffery case, headspaced on the shoulder. The case rims are rebated slightly so as to fit standard belted mag bolt faces. Since the inside diameter of the case head is somewhat larger than that of most belted mag cases, the back thrust will be increased to somewhere around 9,000 pounds. But since these cases are manufactured to better tolerances than are belted cases, I would use the non-belted case for wildcatting, rather than the belted model, even though the back thrust would be greater. Our rifles handle back thrust better than poor headspace….
At one time I was a great fan of the .264 Winchester Magnum. It used a bullet diameter of .264, or 6.5mm, which I thought would be a great combination bullet for varmints and big game. The factory listed the 100 gr. bullet at a velocity of 3700 fps. I had used a .257 Weatherby earlier, only to discover that it would not meet the early day advertised velocity of 3720 fps with a 100 gr. bullet, and even the factory finally conceded that point, dropping the advertised velocity steadily downward to the 3550 fps of today. Therefore, I had great hope for the .264 being much better. That was back when chronographs were coming on the market, and I had just received one from my wife for Christmas.... Don't all wives give that sort of gift to their husbands...? Naturally, the chronograph told stories that were greatly different than what appeared in rifle and cartridge advertisements. The first box of factory .264 ammo with 100 gr. bullets checked out at only 3186 fps! That about blew my mind. I started reloading the cases with loads that would beat that by several hundred feet per second. By the time the velocities reached 3500 fps, all sorts of bolt lift problems, primer pocket expansion, and case head expansion, etc., developed. With a top load of 69 grs. of powder and a 100 gr. Sierra bullet, the velocity was 3525, but the case was expanding .002" on the belt and .005" just ahead on the body. If the case was new, the primer would not leak, but on the second or third loading, leaks showed up. Of course, I had to pound on the bolt to open or close it. By keeping the velocity down to about 3450 fps, things were pretty good, and that became my top usable load. With the 120 gr. bullet I found the top load to be just a bit over 3200 fps with relatively short case life. These loads all produced pressures close to the maximum of 57,200 c.u.p., based on the condition of the cases and primers.
I liked that .264, but not with the problems. My research seemed to indicate that I could build a rifle and use the .30-06 case necked down to .264 and probably get the same, or better, velocities. If so, the back thrust on the bolt would be relieved, too, so I ordered a reamer for the 6.5x06 Ackley Improved, a regular wildcat. To my happy surprise, the 6.5x06 Ackley gives the same top velocities as did the .264, but without case problems and with five or six grains less powder. Had I been more into case design before obtaining the .264 Mag, I might have figured out in advance that the 6.5x06 Ackley would have been the better choice. Isn't it amazing how good hindsight is...?
When you finally decide to start playing around with gun building and cartridge designing, remember to keep your tolerances close, use the smallest case head diameter that will give the performance you are after, and keep all that chamber pressure under control. And keep shooting.
By Bob Jourdan
©Copyright 2010, Precision Shooting Magazine
All handloading manuals take safety very seriously. They cover most of the hazardous points in reloading ammunition in an effort to keep a beginner out of trouble. Some go into detail concerning the strength of brass cases and the importance of using the proper case for the proper loads. They also have some discussion of chamber pressures, advising reloaders what to watch for as they approach top loads that could result in problems. This is all usually done in a good manner, but of course it does not get into deep, technical detail, nor should it. These books are written for reloaders, experienced or beginners, and often refer the readers to other more technical books and manuals for greater detail on the subject. As we all know, any average intelligent shooter can become a proficient ammunition reloader and enjoy the hobby for a lifetime. But as with any consuming hobby, the quest for more knowledge and advancement comes all too soon. Continued success with common factory cartridges often leads the curious minded to start looking at wildcats or improved cartridges, and even the development of some new, personal design that will send off their favorite bullets at the speed of light...or faster. At this point the shooter must investigate the possibilities of case failure and the consequences of excessive chamber pressure.
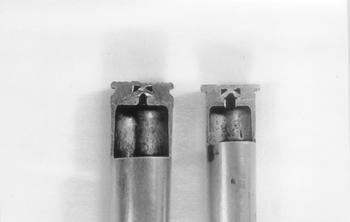
Two extremes, the .300 Weatherby Magnum, (L), and the old-time .30-30 WCF, (R). Notice the thickness of the case web.
One of the most important developments in firearms history was the brass cartridge case that first came onto the scene just before the Civil War. In 1856 a dentist named Maynard patented a brass cartridge case that would expand when fired and seal the rifle chamber to close off any escape of powder gases. This forced all pressure to push behind the bullet and send it out the barrel with the best velocity. Sealing of the chamber was a major step in the development of breech loading rifles. Prior to that, all breech loaders spit a lot of fire and brimstone out the rear of the action into the shooter's face.... They were not any too popular in those days.
With time, shooters wanted more velocity which meant more pressure. When smokeless powders came along in 1886, first in France and then all around the world, pressures began a steady move up. By the turn of the century they had reached the 50,000 c.u.p. (copper units of pressure) that is common today. This copper unit of pressure is simply a description of how chamber pressure came to be gauged by use of a crusher gauge, invented by Alford Noble in about 1860. Small carefully controlled cylinders of soft metal, copper, called "crushers" are placed in a tool attached to the chamber area of a rifle barrel where a hole has been bored through the chamber wall and side wall of a cartridge case. When the cartridge is fired, the high pressure gases push a small piston in the tool up against the copper cylinder, compressing it to some degree. The copper crusher is then measured and the amount of crush length is compared to a compression table to arrive at the pounds of pressure required for that amount of copper compression. Then we use the term, copper units of pressure to relate it to the shooting world.
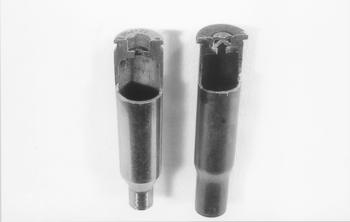
Here we have the .22-250 Remington, (L), and the .30-30, (R). The .22-250 has a two-thickness web, .218" at the outer interior diameter and .195" in the center area about equal in diameter to the primer pocket.
Even though we still use the c.u.p. term for chamber pressures in many publications, there is now an improved system giving pressures in pounds per square inch (psi). It uses electronics to arrive at pressures and is called an electronic-transducer gauge. Instead of crushing a copper piece, a special quartz piece is used because quartz has the property of generating an electrical charge when subjected to mechanical force. This is now known as a piezoelectric transducer, and many loading manuals now list pressures as psi. As reloaders, we must be aware of the significant pressure differences between c.u.p. and psi, with the psi always being much higher. An example would be a .30-06, 150 gr. bullet at 3005 fps for 45,900 c.u.p. or about 58,000 psi. This pressure difference of 12,100 pounds requires your attention. Don't mix c.u.p. with psi.
Good rifle design became very important to contain this pressure, since all chamber seal was provided by the relatively thin brass case. And brass simply can't handle pressures as high as steel can. From this, shooters can see why it is commonly stated that the weak point of any rifle is the brass cartridge case. In a properly designed rifle, the cartridge case will protrude out of the barrel at the breech by about 1/8" before reaching the bolt face. In bad set-ups the distance can be as much as 1/4". With an open gap like that it is easy to see that 50,000 c.u.p. inside the thin brass case can blow it out and release the pressure in the action and shooter's face. Thus, any gunsmith knows, or should know, that the deeper the cartridge is seated into the full cover of the barrel, the safer will be the rifle. Naturally, there must be a way to hook an extractor over the rim of a cartridge to withdraw it from the chamber, and this is where the difference in case head protrusion has to be considered. A large and poorly designed extractor will require the case head to protrude more than would a small, well designed extractor. And in some rifles an extractor cut is required in the barrel. If this cut is made too deep, the cut will expose the thin sidewall of the cartridge case and set up a possible blowout.
It is often stated that a certain case is built stronger than another. In many instances this is true. But in others, it is not. Usually the original cartridge will be designed to handle the pressure of that one particular load. For example, the original .30-30 Winchester cartridge case is designed for pressures in the range of 40,000 c.u.p. This means that the brass is sufficiently thick to handle that amount of pressure in original .30-30 rifle designs. By carefully sectioning the head of a .30-30 case the solid web thickness can be measured and compared to the web thickness of other case designs. My recent measurement showed the .30-30 web to be approximately .182" thick, which means that anytime a cut is made in the barrel breech that exposes more than .182" of the case, the thin wall of the case is all that will be left to hold that 40,000 c.u.p. If a gun designer made a cut of .200" or so to make room for the extractor in the barrel breech and used the .30-30 cartridge case, a disaster would be in the making....
Since the .30-30 was reputed to be a rather weak case, I decided to section a few others to compare their web thicknesses. The .30-06 case showed a web thickness of two dimensions in a Remington case. The center, approximately the diameter of the primer pocket, measured only about .190" thick, while the remainder of the web measured .202". Why they thinned the center around the flash hole, I do not know. Nevertheless, this indicates that any case protrusion of more than .200" from the barrel should be considered dangerous. The maximum product pressure for the .30-06 is listed as 53,200 c.u.p., and that would be exciting if it got loose in the action of your favorite rifle. Since this is a rimless case it is common for the case head to protrude from the barrel breech by some amount, and a few rifles do have a cut made in the barrel to let in an extractor.
A popular varmint cartridge of the day is the .223. It is designed for a maximum product pressure of 55,200 c.u.p., a little hotter than the .30-06, but the case web measures only about .192" thick. This might seem a little inconsistent when compared to the lower pressure and thicker web of the .30-06, but the area inside the .223 case is much smaller than inside the .30-06 and this results in less real pressure working back against the bolt of the .223 in the form of back thrust. The inside chamber pressure is high, however, and therefore the .223 case must be kept to less than .192" unsupported protrusion out of the barrel for safety.
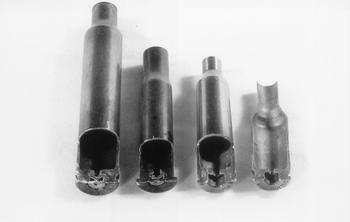
(L-R): .270 Winchester; .30-30 WCF; .22-250 Remington; 6mm BR Norma. The web thicknesses are .202", .182", .218" and .162", respectively.
When I cut into the .300 Weatherby belted case, I expected to find a very thick, substantial web. It turned out to be only a little thicker than the .30-30 and the same as the small .223, measuring .192" thick. Next, I sectioned a .264 Winchester case, made by Winchester, and found it to measure .215" thick at the web and about .200" near the flash hole. It is interesting to find that belted magnum brass may not be any thicker at the web than .30-06 brass, and the chamber pressure of the .300 Weatherby is listed in various places as something around 57,000 c.u.p., or about 7% above that of the .30-06.
A favorite wildcatter's brass is the .284 Winchester rebated case. The web turned out to measure slightly thinner than that of the .30-06 at about .200" thick. Since it is a rimless case, headspacing in the same manner as any other rimless case, it would present the same potential problems with one other added in. That is the fact that it is of the rebated rim type where the rim is the same diameter as that of a .30-06, but the body is much larger starting just ahead of the extractor groove. This will create a larger internal head area which leads to higher back thrust on the bolt when compared to smaller diameter cases with the same chamber pressure. The chamber pressure for the .284 is listed at 57,200 c.u.p., about the same as the .300 Weatherby and the .264 Winchester.
The next case I used for this investigation was the popular benchrest case, 7mm BR, originating from a straight bodied .308 and later from a .300 Savage case. This case is commonly necked down to .25, 6mm or .22 for use in benchrest rifles where pressures are habitually run up considerably above 55,000 c.u.p. The web turned out to be much thinner. My measurements showed the thickest part measuring about .196" and the thin part around the primer pocket only .180" or so in Remington brass. The Norma BR measures only .162" web thickness, and the Lapua BR is .168".
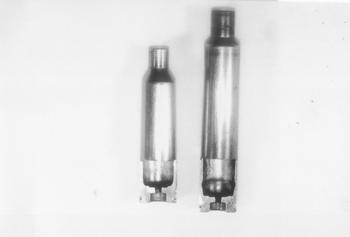
The case on the left is a .270 formed into the 6.5x06 Ackley Improved. Notice the stretch valley just in front of the solid head. The .22-250 case on the right shows no stretching, no thin stretch valley near the web.
These case web measurements are not too informative when we consider that all have been used extensively for wildcatting and all have been successful even with unknown pressures of more than 60,000 c.u.p. This seems to lead to the conclusion that the main concern might well be the method of chambering each wildcat cartridge. If the cartridge is well contained inside the chamber with only a minimum cut for the extractor, it will work well with very high pressures.
Back thrust, mentioned above, brings us to another consideration for cartridge cases used in experimentation or wildcatting. Even though we read of the chamber pressures being in the 50,000 c.u.p. range in most high powered cartridges, it has been proven that back thrust on the bolt is retarded by the fact that the case wall expands to grip the chamber wall, thus holding the case from backing up hard against the bolt. This also indicates that the case head will hold a great deal of pressure by itself, and this is where the web thickness becomes very important. If the gap between the bolt face and the barrel breech is wider than the thickness of the case web, the high chamber pressure inside the case will blow through the thin sidewall in the unsupported gap area. And while we all hear of rifles blowing up, that is not the case. It is rather the loose pressure blowing out from an unsealed chamber when a case failure occurs. As long as the 50,000 c.u.p. plus can be retained inside the chamber, receiver ring and barrel, it is rare that a failure occurs. Steel will contain much more than 50,000 psi, and tests on actions and barrels have proven they will hold more pressure than will the brass case that seals the pressure off. Actions have been tested far beyond 75,000 psi with no failures. The brass, however, will begin to flow at something over 70,000 psi, and will totally fail by the time the pressure reaches 80,000 psi. Then the release of all that pressure inside the receiver, down through the magazine, back through the firing pin hole and into the bolt body is enough to split the stock into kindling wood...among other things. I have the remains of a Mauser M98 action that was totally destroyed with a standard loaded .22-250 cartridge when the headspace became too long, allowing the case to separate. The brass cartridge head was welded into the ejector slot in the locking lug and part of the case body at the end of the web area expanded and formed between the bolt face and the butt of the barrel in a tight manner, looking a lot like it had been melted and poured into the gap. I had to remove the barrel in order to open the action. Incidentally, the shooter ended up in the hospital emergency room for removal of metal and carbon fragments, his eyes being saved by the glasses he was wearing. All of this was brought about by the failure of the brass case when the soft M98 locking lug seats finally pounded back far enough to make the headspace too long. Perhaps I should add here that Mauser actions are not heat treated like our modern factory actions. They are made from relatively soft carbon steel and then only surface hardened, case hardened, for a very thin, hard surface. When these M98s are reconditioned many shops will lap the locking lugs and often will cut the thin, hard surface completely away, leaving only the soft carbon steel underneath to hold the pounding of the bolt locking lugs in the future. They will pound back over a period of time resulting in too much headspace and a wrecked rifle...or worse.
The amount of back thrust on a bolt can be changed to some degree by the design of the cartridge case. Cartridges with considerable taper in the body will produce much more back thrust than will a more straight walled case. To prove this, P.O. Ackley tested the very tapered .250-3000 cartridge in a lever action Savage M99 rifle by loading it up until the case became difficult to extract. This occurred with a load of 34.5 grs. of powder and a 100 gr. bullet to produce a velocity of 2900 fps. At 36 grs. of powder, the action became frozen and required the use of a rod to pound down the barrel while pulling hard on the operating lever to get it open. He then rechambered the rifle for the almost straight tapered case of the .250-3000 Ackley Improved cartridge and loaded it with 36 grs. of powder and a 100 gr. bullet, the very load that previously froze the action. Upon firing, it extracted very easily. He then continued to increase the load until reaching 42 grs. of powder for a velocity of 3400 fps. The action still opened easily. Thus, he had removed most of the back thrust that had originally frozen the action with the tapered, standard case and was able to radically increase the velocity, along with the pressure, without an increase in back thrust by simply removing most of the taper from the case. Today, most experimenters use cases with very little taper for their wildcat creations.
Another interesting test by Ackley was with the .30-30 Ackley Improved cartridge in a M94 lever action Winchester. He found a dry chamber would allow the cartridge case to firmly adhere to the chamber walls; the rifle could be fired with the locking lugs completely removed from the action and only the lever left to hold the bolt shut. The straight walled case did not back out of the chamber, proving that back thrust had been almost completely eliminated by the cartridge case design.
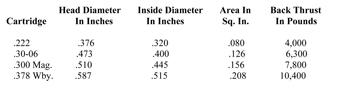
Back thrust is normally figured by multiplying the chamber pressure by the internal area of the cartridge head. It does not equate to chamber pressure as most shooters might think. If it did, then the back thrust of the .223 and the .460 Weatherby would be the same because both are loaded to a chamber pressure of about the same, 55,000 c.u.p. In reality, the .223 has a back thrust of only about 4,025 pounds, while the big .460 has 10,425 pounds, even though the chamber pressures are about the same. Thus, it is readily seen that when given a choice we would much rather have the 4,025 pound load on the bolt face, right near our head, than the 10,425. And this is exactly why we should consider the case we plan to use for our latest wildcat design.
In any chamber the only two parts of a cartridge that are not in some contact with the chamber are the primer and the bullet. The bullet has the barrel opening directly ahead of it, so it will move forward rather easily upon firing the round. The primer is held in the head of the cartridge, in the primer pocket, with only a little friction to secure it. When the cartridge is fired the full pressure developed within the cartridge case will be pushing forward on the bullet base and backward on the case head creating what we call back thrust. Back thrust through the small .080" flash hole has been calculated to be in the 600-800 psi range, and of course the bolt face should be snug against the case head. The primer should be seated slightly below the case head and the initial pressure through the flash hole will push the primer back into solid contact with the bolt face. The pressure inside the case will also work against the case wall to expand it out against the chamber wall. This will cause the case to adhere to the chamber very tightly, preventing the case body from moving back as much as will the case head. Naturally, this results in stretching the brass case slightly and can lead to case head separation. And now, because the bolt and barrel do not make positive contact, it is readily seen that the brass cartridge case head is retaining at least some pressure to prevent it from blowing out in the barrel-bolt gap. Since force is a factor of effective area times pressure, by knowing the area of the inside of the case head we can calculate an approximate back thrust pressure for each cartridge. I say approximate because it would be difficult, if not impossible, to determine back thrust restriction caused by the cartridge case form and adherence to the chamber wall. In other words, back thrust is contained by a combination of the bolt locking lugs and the case clinging to the chamber wall. Ackley's experimentation along these lines proved that a properly designed case will hold back a surprising amount of back thrust from the bolt and locking system of a rifle, but only when the chamber is kept dry. By oiling the chamber or cartridge case before firing, back thrust will be increased tremendously, and may even approach that of full chamber pressure.
Below are examples of back thrust calculations for three cartridge head diameters with equal chamber pressures of 50,000 c.u.p. The chamber wall friction resulting from case configuration is ignored for ease of calculation, and these back pressures are considered to be maximum (see table below).
From this chart it is easy to see that if you plan to use a belted magnum case for your wildcat cartridge, it will produce more than 20% additional back thrust when compared to using a .30-06 case loaded to the same 50,000 c.u.p. chamber pressure. Another way of stating it is that you could increase the load in the .30-06 case to a chamber pressure of 60,000 c.u.p. and still have less back thrust on your bolt than if using the magnum case at only 50,000 c.u.p. And this is one reason why it is so often fruitless to use the belted case for your brain child, lightning striking wildcat....
In recent years the ammunition companies have been avoiding the use of belted cartridge cases for new magnum designs. They have moved to the smooth bodies, no belts, of variations of the old .404 Jeffery case, headspaced on the shoulder. The case rims are rebated slightly so as to fit standard belted mag bolt faces. Since the inside diameter of the case head is somewhat larger than that of most belted mag cases, the back thrust will be increased to somewhere around 9,000 pounds. But since these cases are manufactured to better tolerances than are belted cases, I would use the non-belted case for wildcatting, rather than the belted model, even though the back thrust would be greater. Our rifles handle back thrust better than poor headspace….
At one time I was a great fan of the .264 Winchester Magnum. It used a bullet diameter of .264, or 6.5mm, which I thought would be a great combination bullet for varmints and big game. The factory listed the 100 gr. bullet at a velocity of 3700 fps. I had used a .257 Weatherby earlier, only to discover that it would not meet the early day advertised velocity of 3720 fps with a 100 gr. bullet, and even the factory finally conceded that point, dropping the advertised velocity steadily downward to the 3550 fps of today. Therefore, I had great hope for the .264 being much better. That was back when chronographs were coming on the market, and I had just received one from my wife for Christmas.... Don't all wives give that sort of gift to their husbands...? Naturally, the chronograph told stories that were greatly different than what appeared in rifle and cartridge advertisements. The first box of factory .264 ammo with 100 gr. bullets checked out at only 3186 fps! That about blew my mind. I started reloading the cases with loads that would beat that by several hundred feet per second. By the time the velocities reached 3500 fps, all sorts of bolt lift problems, primer pocket expansion, and case head expansion, etc., developed. With a top load of 69 grs. of powder and a 100 gr. Sierra bullet, the velocity was 3525, but the case was expanding .002" on the belt and .005" just ahead on the body. If the case was new, the primer would not leak, but on the second or third loading, leaks showed up. Of course, I had to pound on the bolt to open or close it. By keeping the velocity down to about 3450 fps, things were pretty good, and that became my top usable load. With the 120 gr. bullet I found the top load to be just a bit over 3200 fps with relatively short case life. These loads all produced pressures close to the maximum of 57,200 c.u.p., based on the condition of the cases and primers.
I liked that .264, but not with the problems. My research seemed to indicate that I could build a rifle and use the .30-06 case necked down to .264 and probably get the same, or better, velocities. If so, the back thrust on the bolt would be relieved, too, so I ordered a reamer for the 6.5x06 Ackley Improved, a regular wildcat. To my happy surprise, the 6.5x06 Ackley gives the same top velocities as did the .264, but without case problems and with five or six grains less powder. Had I been more into case design before obtaining the .264 Mag, I might have figured out in advance that the 6.5x06 Ackley would have been the better choice. Isn't it amazing how good hindsight is...?
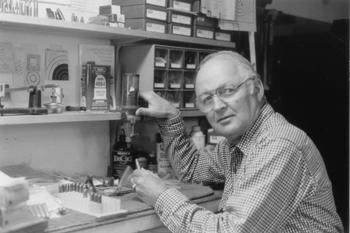
When you finally decide to start playing around with gun building and cartridge designing, remember to keep your tolerances close, use the smallest case head diameter that will give the performance you are after, and keep all that chamber pressure under control. And keep shooting.